UV ink printing usually adopts the method of instant UV drying, so that the ink can quickly adhere to the surface of the film self-adhesive material. However, in the process of printing, the problem of poor adhesion of UV ink on the surface of film self-adhesive materials often occurs.
What is the poor adhesion of UV ink?
Different terminals have different methods for testing poor adhesion of UV ink. However, in the self-adhesive label industry, most customers will use 3M 810 or 3M 610 tape for ink adhesion test.
Evaluation criteria: The ink firmness is evaluated according to the amount of ink stuck after the adhesive tape is stuck on the label surface and then removed.
Level 1: no ink falling off
Level 2: A little ink falls off (<10%)
Level 3: medium ink shedding (10%~30%)
Level 4: serious ink shedding (30%~60%)
Level 5: almost all the ink falls off (>60%)
question 1:
In production, we often encounter the problem that when some materials are printed normally, the ink adhesion is OK, but after the printing speed is improved, the ink adhesion becomes worse.
cause1:
As the photoinitiator in the UV ink absorbs the UV light to produce free radicals, it will cross link with the monomer prepolymer in the ink component to form a network structure, which is a transient process from liquid to solid. However, in actual printing, although the ink surface dried instantly, it was difficult for ultraviolet light to penetrate the solidified ink surface layer to reach the bottom layer, resulting in incomplete photochemical reaction of the bottom layer ink.
Suggestion: For deep ink and light printing, high color strength ink can be used to reduce the thickness of the ink layer, which can not only ensure the dryness of single-layer ink, but also effectively improve the production efficiency.
cause2:
The UV mercury lamp is generally used for about 1000 hours, and it can be lit after the UV lamp has been used for more than 1000 hours, but the UV ink cannot be completely dry. In fact, once the UV lamp has reached its service life, its spectral curve has changed. The ultraviolet light emitted does not meet the requirements of dry ink, and the infrared energy has increased, resulting in material deformation and ink embrittlement due to high temperature.
Suggestion: The use time of UV lamp should be recorded correctly and replaced in time. During normal production, it is also necessary to regularly check the cleanliness of the UV lamp and clean the reflector. Generally, only 1/3 of the UV lamp's energy directly shines on the material surface, and 2/3 of the energy is reflected by the reflector.
question 2:
In production, we often encounter the problem that when some materials are printed normally, the ink adhesion is OK, but after the printing speed is improved, the ink adhesion becomes worse.
Cause 1:
The short contact time between ink and substrate leads to insufficient molecular level connection between particles, affecting adhesion
The particles of the ink and the substrate diffuse and connect with each other to form a molecular level connection. By increasing the contact time between the ink and the substrate before drying, the connection effect between molecules can be more significant, thus increasing the ink adhesion.
Suggestion: slow down the printing speed, make the ink fully contact with the substrate, and improve the ink adhesion.
Cause 2:
insufficient UV light exposure time, resulting in ink not completely dry, affecting adhesion
The increase of printing speed will also shorten the irradiation time of UV light, which will reduce the energy that shines on the ink, thus affecting the drying condition of the ink, resulting in poor adhesion due to incomplete drying.
Suggestion: Slow down the printing speed, let the ink fully dry under the UV light, and improve the adhesion.
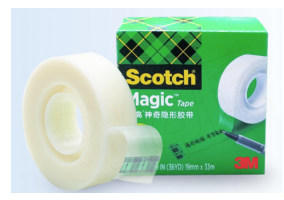
Post time: Oct-09-2022